- INTRODUCTION
- Instruments Or Drawing
- Basic Instruments
- Drawing board
- Drawing sheet
- Drawing pencil
- Drawing clips or pins
- Eraser
- Eraser shield
- Instruments for Drawing Straight Lines
- T- square
- Set- squares
- Instruments For Drawing Curved Lines
- Large size compass
- Small bow compass
- French curve
- Instruments For Measuring Distance
- Large size divider
- Small bow divider
- Scales
- Instruments For Measuring Angles
- Protractors
- Set-squares
- Special Tool
- Mini drafter
- Drawing Board :- A drawing board with its working surface upward. The top surface of the board is perfectly smooth and level. The bottom of the drawing board. A drawing board is rectangular in shape and is made of well seasoned soft wood such as oak or pine. A straight ebony edge is fitted on the left side on the board against which the head of the T- square moves.
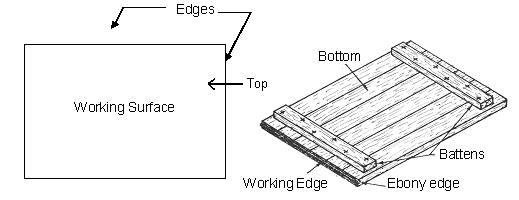
Drawing Board (Top) Drawing Board (Bottom)
- Drawing Sheet :- The drawing is frequently made in pencil on the drawing sheet. The best drawing sheet has the following qualities:
- Light cream buff in colour to have good appearance
- Fine grains to pick up the graphite and produce clean, dense black lines
- Strong fibers
- Superior erasing qualities
- Folding strength
- Toughness
- Smooth surface
- Hard surface
- Drawing Pencil :- Neatness, quality and accuracy of the drawing greatly depends upon the type and conditions of the pencil used for drawing. Pencil leads are made of graphite with clay added in varying amounts to make 18 grades from 9H to 7B. These grades can be divided in three groups:
- Hard : 9H to 4H
- Medium : 3H to B (3H, 2H, H, F, HB and B)
- Soft : 2B to 7B
- 2H Pencil - For drawing outlines, Centre lines, Break lines, etc.
- H Pencil - For dimensioning, arrowheads, hatching lines, lettering, sketching, circles, arcs, etc.
- Micro tip pencil - 0.5 mm for drawing outlines and 0.8 mm for shading and sketching
- Drawing Clips Or Pins :- Drawing clips or pins are used to fix the drawing sheet on the drawing board at the required place. Frequent use of pins cause formation of impressions of pin pricks on the board, thus spoiling the surface of the board. The present trend is to go in for steel clips, if the size of the drawing paper is the same as that of the drawing board. Clips are used at all the four corners of the drawing board to clamp the paper. Adhesive tapes are also used for fixing the drawing sheet.
- Eraser :- Eraser is used to remove the extra lines, lines/marks drawn by mistake and to clear soiled spots on the drawing. Only pencil eraser is used. Soft India-rubber is the most suitable kind of eraser for pencil drawings. The eraser used should be such that the surface of the drawing paper is not spoiled in anyway. It is desirable to use erasing shield to protect the near by lines from being erased. The rubber crumbs formed after erasing should be swept away with a clean duster and should never be brushed off with hands. Use of eraser should be minimized by proper planning.
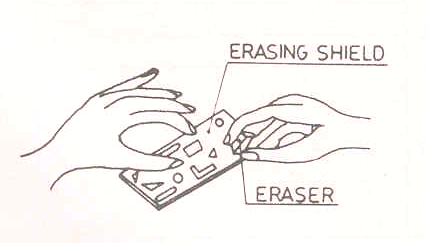
- Erasing Shield :- It is a thin metal or plastic plate cut with slots, circles and curves of different dimensions. It helps to erase unwanted pencil lines without erasing the surrounding lines.
- T- Square :- It is composed of a long strip called blade, which is screwed rigidly at right angle to a shorter piece called head or stock. It is made of mahogany or pear wood, which is harder than the board wood. The head also has an ebony edge which slides against the working edge of the board. T- Square is used for making horizontal, vertical, inclined or parallel lines on the drawing sheet.
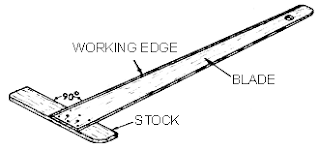
- Set-Squares :- Set-squares are made of transparent plastic and are available in the shape of triangles, having a French curve or simply a gap cut in the body. These are used for drawing short straight lines, measuring and drawing certain angles. A good combination of set-squares is 30O x 60O set square with a long edge of 250 mm and a 45O set squares with each edge of 200 mm.
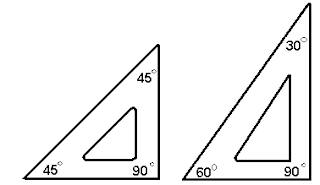
- Large Size Compass :- The compass is used for drawing circles and arcs. It consists of two legs hinged together at its upper end. A pointed needle is fitted at the lower end of one leg, while a pencil lead is inserted at the end of the other leg. The lower part of the pencil leg is detachable and it can be interchanged with a similar piece containing an inking pen. Both the legs are provided with knee joints. Circles up to about 120 mm diameter can be drawn with the legs of the compass kept straight. For drawing smaller circles, both the legs should be bent at the knee joints so that these are perpendicular to the surface of the paper.
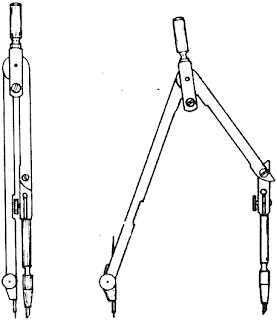
- Small Bow Compass :- Small bow compass is conveniently used for drawing circles and arcs of small diameters. It is very handy when a number of small circles of the same diameter are to be drawn. The adjusting nut of the small compass may be on the side or at the centre. This adjusting nut is provided to make fine adjustment for accurate small circles.
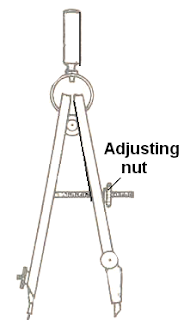
- French Curves :- French curves are used to draw irregular curved lines, which can not be drawn with a compass. A light pencil curve is first drawn free hand through the known points. Neat continuous curve is finally drawn with the longest possible curve coinciding exactly with the free hand curve. Proper care must be taken to ensure that no corners are formed anywhere on the curve. Proper use of French curves requires skill. French curves are made of transparent celluloid or plastic. These are available in various shapes. One of the french curves.
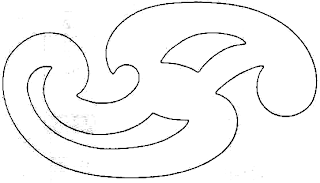
- Large Size Divider :- The dividers has two legs hinged at the upper end and is provided with steel pins at both the lower ends, but it does not have the knee joints.

- The dividers are used to
- Divide straight or curved lines into desired number of equal parts.
- Set off distances from the scale to the drawings.
- Transfer measurements from one part of the drawing to another.
- Small Bow Divider :- The small bow divider is adjusted by a nut and is very convenient for marking minute divisions and large number of short equal distances.
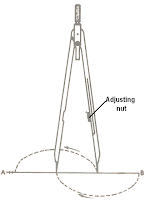
- Scales :- Scales are made of wood, steel, celluloid or plastic. Stainless steel scales are more durable. Scale may be flat or of triangular cross- section. 15 cm long and 2 cm wide or 30 cm long or 3 cm wide flat scales are commonly used. These are usually about 1 mm thick. The longer edges of the scale are marked with inch and its sub-divisions on one side and centimeter and its sub-divisions on the other side.
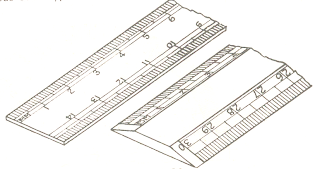
- Protractors :- Protractors or Pro-circles are used for drawing any desired angle. These are made of hard transparent plastic. The edges are either squared or beveled. Semi-circular type protractor.
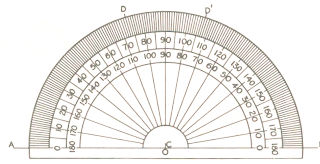
- Mini Drafter :- A T-square, protractor and set squares can be replaced by a drawing drafter. With this, lines can be drawn at any desired angle. A mini drafter is made with several links. The scale is attached at the working end of the links. The scale unit can be rotated and set at any desired angle. The clamp end is fixed to the upper or lower edge of the drawing board. There is no need to have a working edge on a drawing board when a mini drafter is used. Mini drafter saves considerable time.
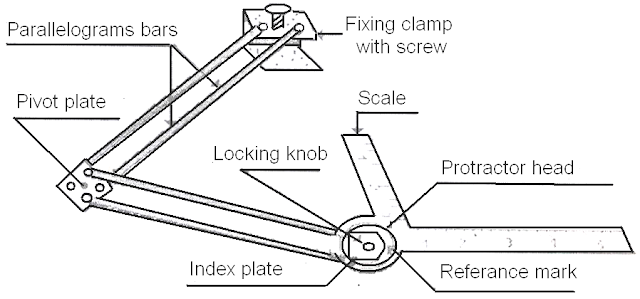
- Guidelines For Use :- The mini drafter is clamped on the board for use as follows :
- Set the protractor head such that zero on protractor coincides with the reference mark on index plate. Lock the head by locking knob.
- Insert the clamp at the left-top corner of the drawing board along horizontal or vertical edge.
- Align the bottom of horizontal scale along the bottom edge of the board. In this position tighten the clamp screw.
- Place the drawing sheet, with already drawn border lines, underneath the scales of mini drafter and align the bottom borderline of sheet with the edge of horizontal scale of mini drafter.
- Fix the drawing sheet in the same position by drawing clips or adhesive tape.
- The protractor head along with scales can be moved to any place on the drawing sheet.
- To draw horizontal and vertical line the reference mark should coincide with the zero on protractor head. To draw inclined line the protractor can be set to any desired angle coinciding with the reference mark on the index plate.
- All the positioning is done by one hand while the other is used for drawing the lines.
- Precautions for Neatness in Drawing Work :- Cleanliness and neatness in drawing work are very important requirements. Following precautions are required to be taken to keep a drawing neat and clean:
- The hands should be kept clean at all times during work.
- All the drawing instruments should be kept clean by wiping with a cloth/towel.
- Special emphasis is to be given to sliding instruments on the drawing sheet, such as T- square and set squares. These instruments must be cleaned properly every time.
- Pencil should always be kept sharp and used properly. It should be sharpened away from the drawing sheet and other instruments.
- Dirt and graphite particles from the pencil will make the drawing dirty. Hence, every care should be taken to remove them from the drawing sheet.
- Direct contact of hand with the drawing sheet should be avoided.
- Rubbing or erasing should be done properly with soft eraser.
- Write the name of any 10 drawing instruments?
- What are the sizes of drawing boards used for sheet sizes A0, A1, A2 and A3?
- Draw the following angles by using T-square and Set squares :- 15⁰, 30⁰, 45⁰, 60⁰, 75⁰, 90⁰, 105⁰, 120⁰, 135⁰, 150⁰ and 165⁰?
- Draw the following angles with protractor :- 17⁰, 34⁰, 36⁰, 51⁰, 72⁰, 81⁰, 89⁰, 102⁰, 162⁰, and 178⁰?
- What are the uses of a mini-drafter. Draw the following angles with the help of a mini-drafter :- 11⁰, 22⁰, 33⁰, 44⁰, 55⁰, 66⁰, 77⁰, 88⁰, 101⁰, 114⁰, 127⁰, 141⁰, and 155⁰?
- Draw a name block as per ISI, for drawing sheet?
- Draw a layout of following drawing sheets :- A1 and A2 using reducing scale (1:5)?
- Draw a circle of 40 mm radius and divide it into 6 equal parts with the help of 30⁰-90⁰-60⁰ set square and T-square and mini-drafter?
- Write the surface area and trimmed size of drawing sheets A0, A1, A2 and A3 sizes?
- Draw a circle of 50 mm radius and divide into 8 equal parts by using a 45⁰-set square?
- Name the different gratings of pencils?
- What are the uses of the following :- Drawing board, T-Square, Set Square, Protractor, Scales?
- What is a mini drafter and when it is used?
- Name a single instrument which can serve the purpose of T-Square, Set Square, Protractor and Scale?
- Name the instruments used to draw :- Circle, Angle, Vertical Lines, Horizontal Lines, Parallel Lines, Marking Distances?
- What information a title block gives?